Ein technisches Denkmal im Herzen des Schachtgeländes
Im Innenhof des Hauptgebäudes des Arno-Lippmann-Schachts befindet sich ein besonderes technisches Denkmal: die original erhaltene Fördermaschine aus DDR-Zeiten. Seit 2002 ist sie durch ein eigens errichtetes Schutzhaus vor Witterungseinflüssen geschützt. Das eingeschossige Gebäude mit seinem flach geneigten Satteldach und großen Fensterflächen ermöglicht Besucherinnen und Besuchern einen freien Blick auf die Anlage – auch von außen.
Die Fördermaschine ist eine sogenannte Trommelfördermaschine, die ab 1983 im Einsatz war. Gefertigt wurde sie vom VEB NOBAS Nordhausen. Die beeindruckende Fördertrommel misst 4 Meter im Durchmesser und 1,65 Meter in der Breite. Ein 520-Volt-Gleichstrommotor mit 450 Kilowatt Leistung sorgte für den Antrieb. Damit erreichte die Maschine eine Drehzahl von 29 Umdrehungen pro Minute.
Je nach Einsatzzweck war eine Fördergeschwindigkeit von bis zu 6 Metern pro Sekunde bei der Seilfahrt (Personentransport) und 4 Metern pro Sekunde beim Materialtransport möglich.
Die Seiltrommel mit Bremsapparat
Zum Herzstück der Förderanlage des AL-Schachtes gehörten neben der Fördermaschine die Seiltrommel und die dazugehörige Bremsanlage. Diese wurden – ebenso wie die bis 1983 verbaute Fördermaschine – vom damaligen VEB Schwermaschinenbau NOBAS Nordhausen hergestellt.
Die Trommel hatte einen Durchmesser von vier Metern und bestand aus zwei mechanisch gekoppelten Trommelhälften, auf denen die Seile jeweils entgegengesetzt auf- bzw. abgewickelt wurden, um die gegenläufige Bewegung der Fördergefäße zu realisieren.
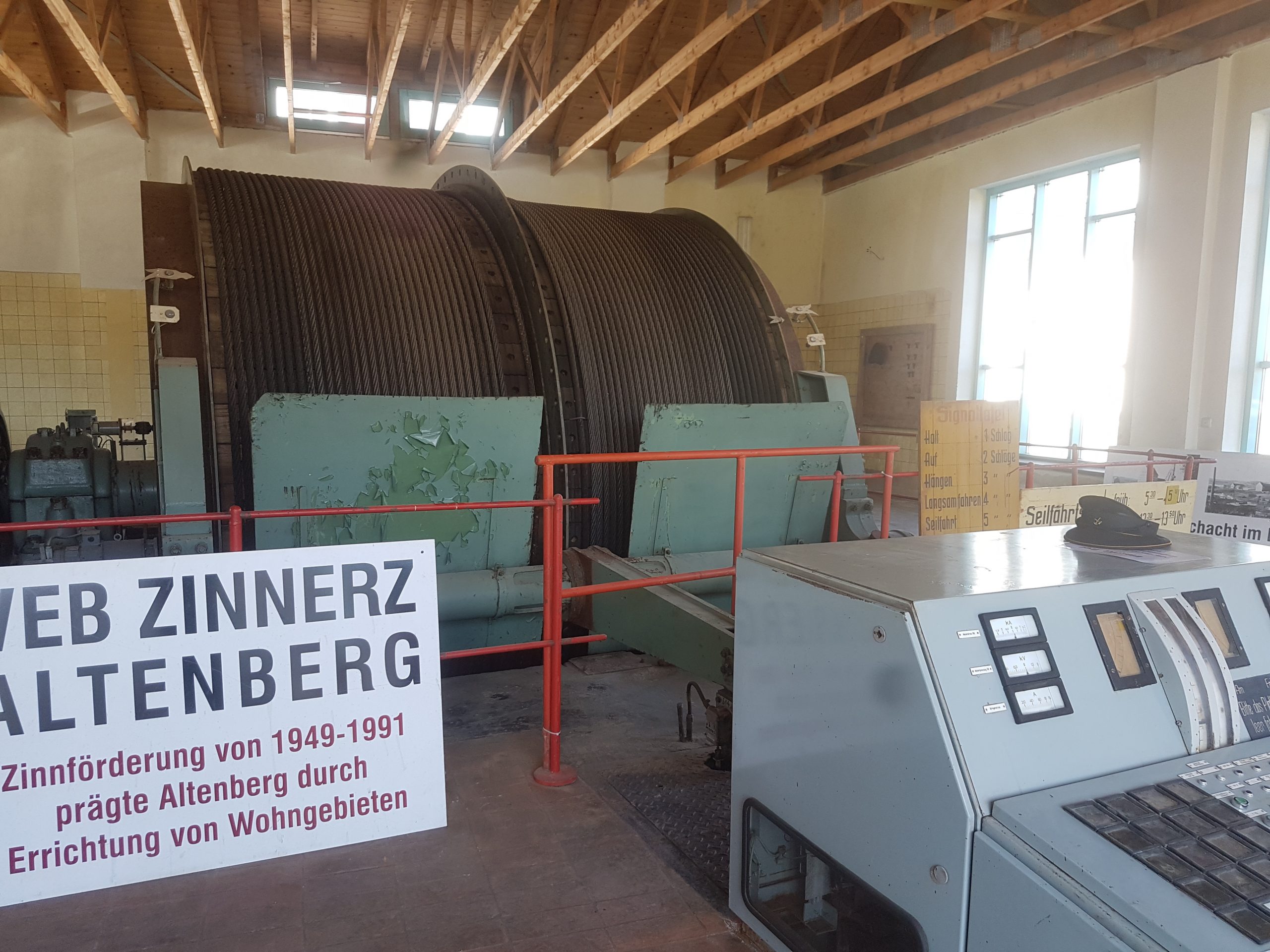
Im Jahr 1983, im Zuge der umfassenden Rekonstruktion der gesamten Schachtförderanlage, wurden neben der Maschine auch die Seiltrommel ausgetauscht. Die neue Seiltrommel hatte die gleichen Maße wie die alte und bestand ebenfalls aus zwei miteinander gekoppelten Trommelhälften. Bei Materialfahrten konnten diese mechanisch getrennt werden, sodass nur die Trommelhälfte genutzt wurde, die direkt mit der Maschine verbunden war.
Grund für den Austausch der Seiltrommel waren Alterserscheinungen nach 20 Jahren Betrieb. Im Inneren der Trommel hatten sich Risse gebildet, die mehrfach geschweißt werden mussten. Mit der Erhöhung der Nutzlast der Skipgefäße durch die neue Fördermaschine von 4,6 auf 6 Tonnen befürchtete man eine Gefährdung der Betriebssicherheit – insbesondere bei einem Notstopp der Anlage im Falle einer Störung, da hierbei eine höhere Krafteinwirkung auf die Seiltrommel entsteht. Für den Austausch wurde damals das Dach des Maschinengebäudes geöffnet.
Zur Anlage gehörte außerdem der pneumatische Bremsapparat, der nahezu vollständig und im Originalzustand im Keller des Maschinengebäudes erhalten ist. Auch dieser wurde von NOBAS geliefert. Über einen großen Druckluftzylinder, der über Umlenkhebel zur Krafterhöhung die Bremsbacken an der Seiltrommel betätigte, konnte der Maschinist die Anlage pneumatisch bremsen.
Während der Seilfahrten bzw. Zwischenseilfahrten wurde die Bremse durch die Fördermaschinisten manuell betätigt. Bei der vollautomatischen Erzförderung hingegen erfolgte die Betätigung der Bremse vollautomatisch über elektropneumatische Ventile.
Zu guter Letzt verfügte die Anlage über eine Notbremseinrichtung: Bei Störungen oder einem Ausfall der Druckluftversorgung wurde die Bremse durch ein über eine Tonne schweres Notgewicht mechanisch vollständig angelegt. Voraussetzung für die Reaktivierung der Fördermaschine durch die IG AL-Schacht war daher auch das Lösen der Bremse – was durch mechanisches Anheben des Notgewichts erreicht wurde.
Pult und Grafik
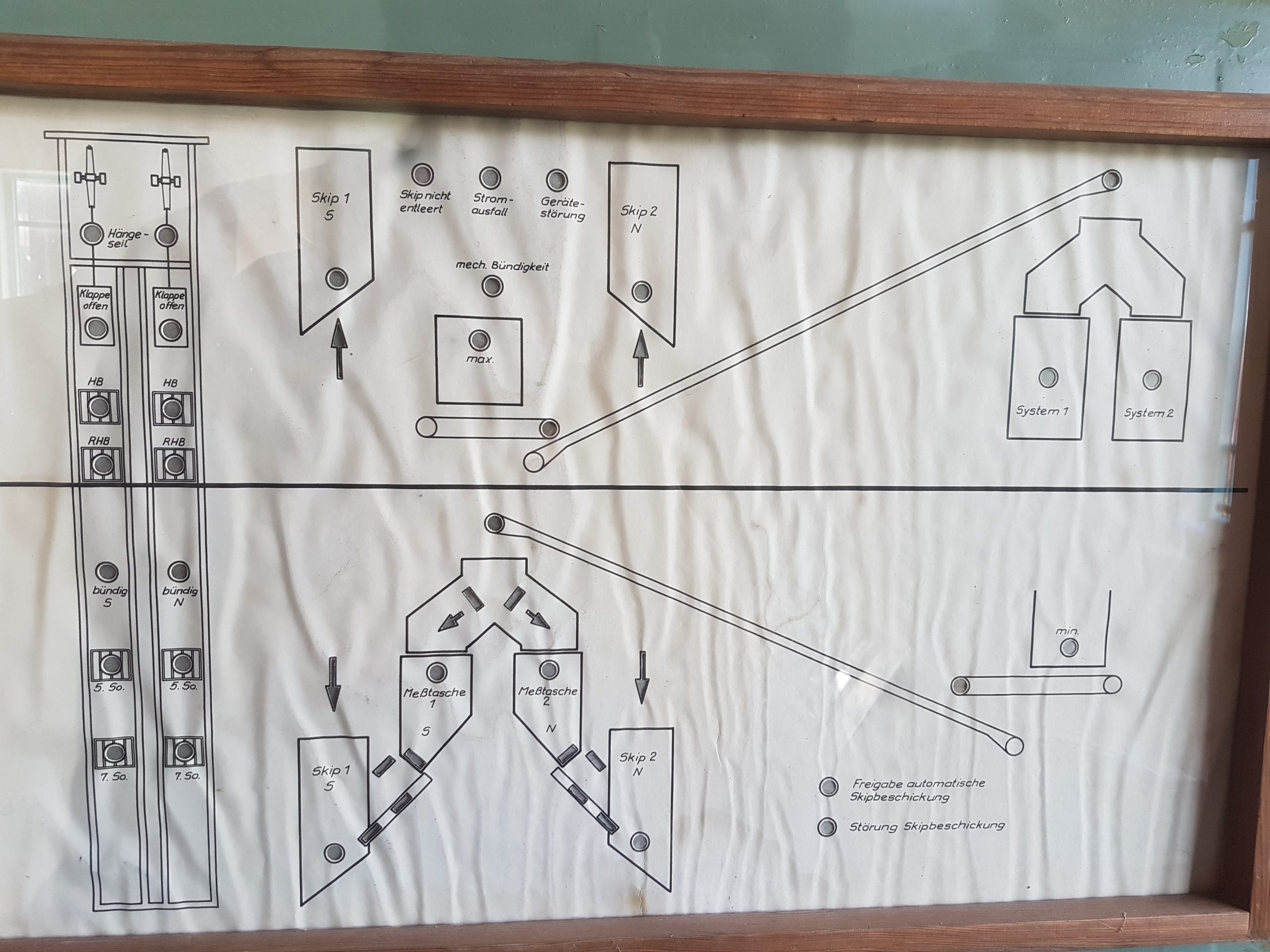
Die Grafikanzeige diente dem Maschinisten zur Verfolgung des automatischen Förderprozesses sowie zur schnellen Fehleranalyse im Störungsfall. Sie unterteilte sich in drei Bereiche: Untertage, Schachtbereich und Übertage.
Im Untertagebereich wurde die Befüllung der Messtaschen durch Gummiförderbänder und Plattenbänder mit Roherz überwacht und grafisch dargestellt. Die Messtaschen wogen das Erz jeweils zu 6 Tonnen ab – auf diese Fördermenge waren sowohl der Skip als auch die Fördermaschine ausgelegt. Anschließend wurde die automatische Befüllung des Skips überwacht.
Sobald der Skip befüllt war, wurde ein Signal erzeugt, das die Abfahrbereitschaft meldete. Sofern keine Störung vorlag, wurde der Skip durch die automatisch arbeitende Fördermaschine in den Übertagebereich gefördert – dies wurde im zweiten Teil der Grafik dargestellt.
Darüber hinaus zeigte die Grafikanzeige auch die wichtigsten Sicherheitseinrichtungen im Schacht an, beispielsweise alle Schachttore und Stromversorgungen.
Ist der Skip im Übertagebereich angekommen, fährt er automatisch in die Entleerungseinrichtung ein und kippt seinen Inhalt in den Übertagebunker. Die vollständige Entleerung wurde mit einer radiometrischen Schranke überwacht, da jede andere Form der Kontrolle entweder nicht zuverlässig möglich oder zu störanfällig war.
Das geförderte Roherz war nicht immer trocken – teilweise wurde regelrechter Schlamm gefördert. Wenn das Erz von der Brecherei aus diesem Grund nicht abgenommen werden konnte, wurde der automatische Förderprozess vorübergehend gestoppt.
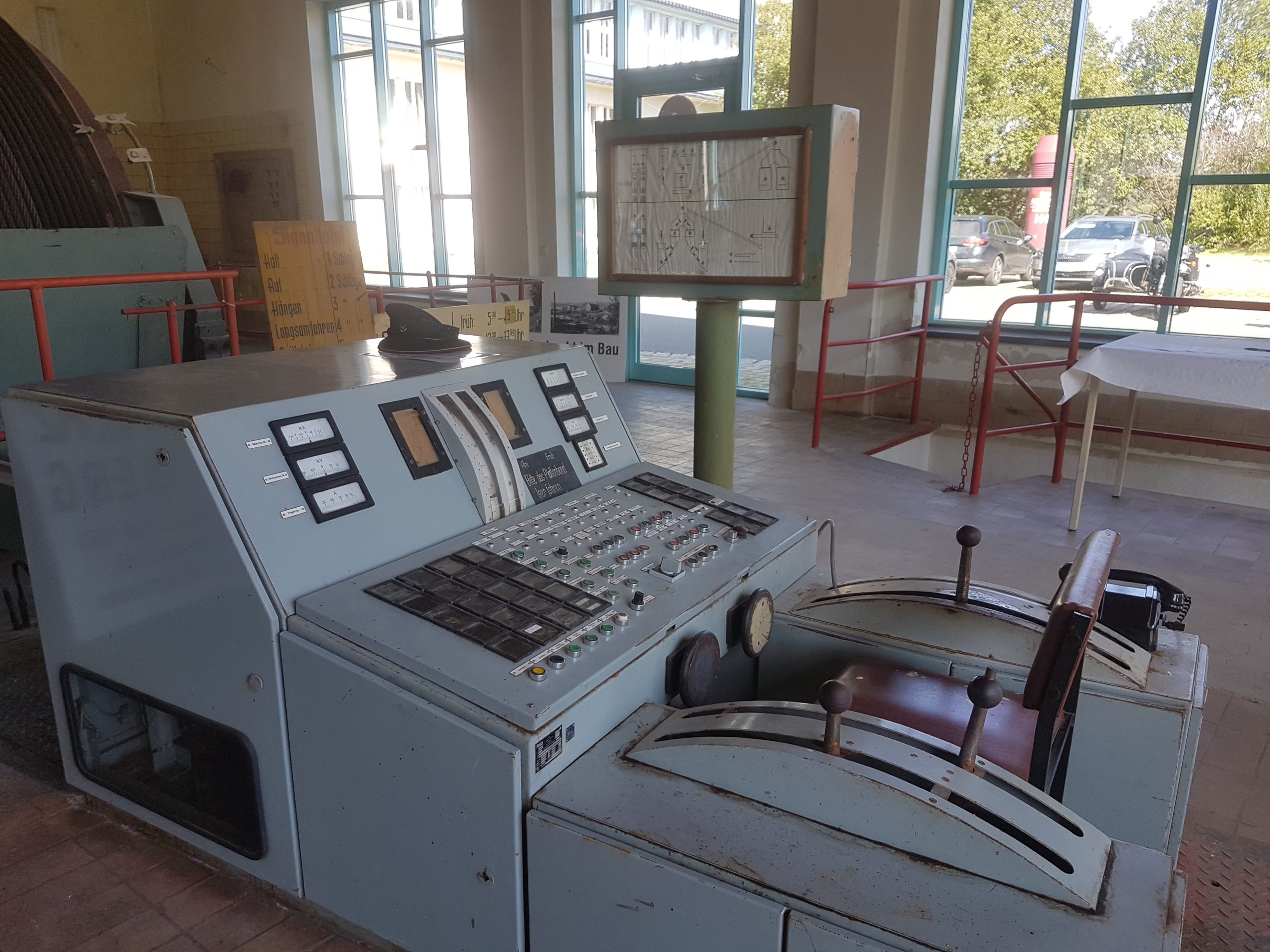
Der Fördermaschinen Motor
Der Motor, der die Seiltrommel antreibt, ist ein fremderregter, fremdgekühlter Gleichstrommotor mit eine Nennleistung von 450 kW und 29 U/min, gebaut im Sachsenwerk Dresden mit der Nummer 2310995 / 1983. Die Nennspannung des Motors beträgt 520 V Gleichspannung und der Nennstrom beträgt 1025 A – eine „Überlast“ bis 2000 A war kurzeitig möglich, musste jedoch manuell freigegeben werden.
Im Sommer 1983 wurde der Motor im Rahmen des Projektes „REKO Schachtfördermaschine“ anstelle des bis dahin verwendeten Leonardsatzes mit 320 kW Leistung zusammen mit der neuen Seiltrommel in nur 4 Wochen eingebaut.
Geregelt wurde die Drehzahl des Motors von einer Tyristorregelung vom VEB Kombinat Elektroprojekt und Anlagenbau Berlin, bestück mit Thyristoren der Firma TESLA . Die Drehzahl und die Drehrichtung gab der Fördermaschinist vom Bedienpult aus vor bzw. sie wurde vom Automatikmodus welcher bei der Erzförderung eingeschaltet wurde, an Hand von verschiedenen Sensor- und Gebedaten vorgegeben. Die Drehzahl konnte in beide Drehrichtungen von 0 bis zur maximalen Drehzahl von 29 U/min geregelt werden. Die Regelung selbst war in dem angrenzenden Gebäude der Trafostation untergebracht. Die Regelung wurde bei der Demontage ab 1993 abgebaut und verschrottet. Unterlagen zu dieser Regelung wurden bisher nicht gefunden.
Der Stator der Maschine mit einem Durchmesser von ca. 3,5 m besteht aus 2 Halbschalen die zur Montage/Demontage des Ankers getrennt werden konnten. Der Motor ist eine 12 polige Ausführung mit zusätzlichen Wendepolen und Kompensationswicklungen.
Der Anker des Motors hat einen Durchmesser von 1990 mm und wiegt ca. 14 t. Das Blechpaket des Ankers (Rotor) ist 1020 mm lang. Die Ankerwelle hat 30 cm Durchmesser. Der Lagersitz auf der Kommutatorseite des Ankers hat 250 mm Durchmesser und eine Länge von 300 mm. Gelagert wird die Welle in einem mit Öl befülltem Gleitlager.
Auf der Gegenseite (Abtriebsseite) hat der Anker keinen Lagersitz. Dort ist eine starre Bolzenkupplung, Durchmesser 870 mm mit 10 Kupplungsbolzen je 70 mm Durchmesser montiert. Damit wurde der Anker mit dem Gegenstück der Kupplung, welches auf das aus dem Gleitlager der Seiltrommel herausstehenden Wellende montiert ist, starr verbunden.
Dieses Lager hatte also eine Doppelfunktion, einerseits wurde dort die Seiltrommel gelagert andererseits die Abtriebsseite des Motors. Die sehr genaue Ausrichtung von Motor und Seiltrommel ist deshalb extrem wichtig. Die Stützweite dieser beiden Lager beträgt 2760 mm
Der auf der Ankerwelle montierte Kommutator (mechanischer Stromwender) hat einen Durchmesser von 1200 mm und eine Länge von140 mm. Er besteht aus 560 Lamellen an die die Wellenwicklung des Ankers angeschlossen ist.
Der Ankerstrom wird mittels 12 Bürstenblöcken über den Kommutator auf die Ankerwicklung geführt. Ein Bürstenblock besteht aus 6 einzelnen Kohlebürsten vom Typ E14D, der Abmessung 12.5 x 32 x 40 mm, hergestellt bei der Firma VEB Elektrokohle Lichtenberg (EKL). Es sind 3 Kohlen nebeneinander und 2 Kohlen hintereinander angeordnet. Die Bürsten werden von den am Stator befestigten Bürstenhaltern über ringförmig angeordnete Stromschienen mit Strom versorgt. Diese Stromschienen sind wie der Stator jeweils in zwei Hälften teilbar. Die Schleiflänge der Bürsten beträgt 110 mm.
Die für den fremdluftgekühlten Motor notwendige Kühlluft wurde von einem im Keller aufgestellten Gebläse erzeugt und über Kanäle dem Motor zugeführt.
Das Gesamtgewicht des Motors beträgt 44,9 t – der Stator wiegt 30,9 t und der Anker 14 t.
Da kaum Erfahrung mit großen tyristogeregelten Motoren und den damit verbundenen Belastung der Wickelköpfe des Ankers durch Oberwellen vorlagen wurde zum Motor ein identischer Ersatzanker geliefert. Der Anker wurde aber bis zur Einstellung der Föderbetriebes am 28.03.1991 nicht benötigt und steht heute noch neben dem Motor auf dem Transportgestell.
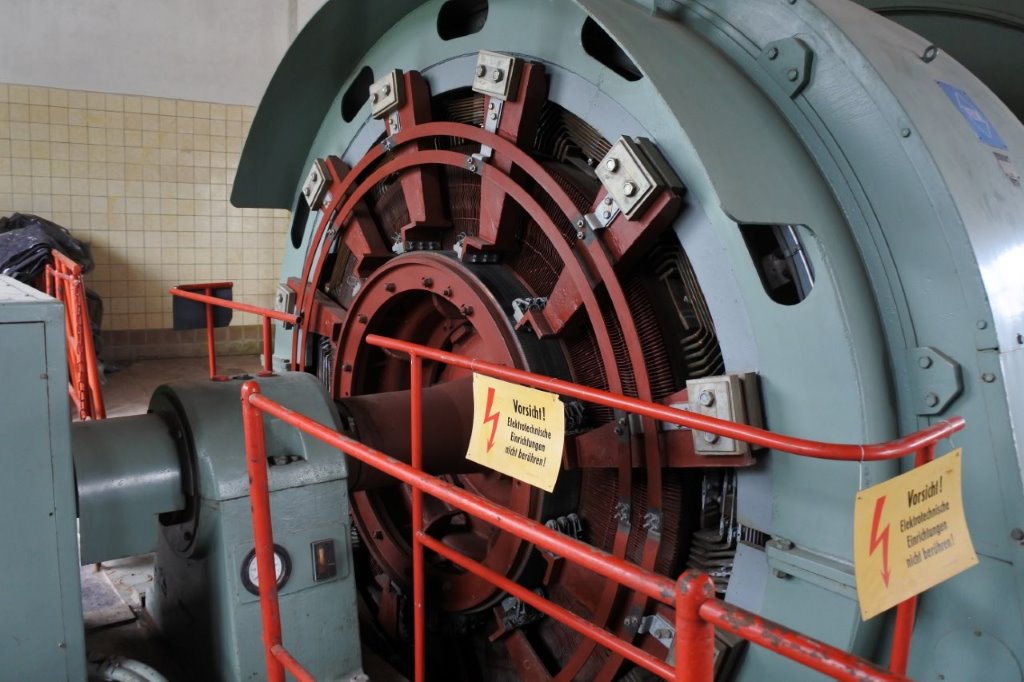
Technische Daten des Fördermaschinen Motors:
- Fremderregter, fremdgekühlter Gleichstrommotor, thyristorgesteuert (Steuerung von TESLA nicht mehr vorhanden)
- Hersteller: VEB Elektromaschinebau Sachsenwerk
- Typ. GMFFP 1923 – 29
- Nr.: 2310995 / 1983
- Norm: TGL 20675
- Nennspannung: 520 V DC
- Nennstrom: 1075 A
- Maximalstrom: 2000 A
- Nennleistung: 450 kW
- Nenndrehzahl: 29 U/min
- Bauform: IM 7115
- Schutzgrad: Kommutatorseite (N-Seite) IP00 Abtriebsseite (D- Seite) IP30
- Wärmebeständigkeitsklasse: WBK E (120C°)
- Erregerspannung: 235 V DC
- Erregerstrom: 60 A
- Erregerleistung: 14,1 kW
- notwendiger Kühlluftstrom: 350 m³/h
- notwendiger Kühlluftstromdruck: 700 Pa
- Ankerdurchmesser: 1880 mm
- Ankerumfang: 5900 mm
- Ankerlänge: 910 mm (Blechpaketlänge)
- Kommutatordurchmesser: 1200 mm
- Kommutatorumfang: 3800 mm
- Kommutatorlänge: 140 mm
- Anzahl Kommutatorlammellen: 560
- Schleifbreite der Bürsten: 110 mm
- Anzahl Bürstenpakete: 12
- Anzahl Bürsten pro Paket: 6 (3 nebeneinander, 2 hintereinander)
- Bürstentyp: E20 D
- Bürstenabmessung: 32 x 12,5 mm (400 mm²)
- Bürstenlänge: ca. 40 mm
- Gesamtschleiffläche pro Bürstenbaket: 2400 mm²
- Bürstenhersteller: VEB Elektrokohle Lichtenberg (EKL)
- Querschnitt Kupferschienensystem
- Stromzuführung zu den Bürsten: 40 x 6 mm
- Anzahl Hauptpole: 12
- Anzahle der Nuten für die Kompensationswicklungen in den Hauptpolen: 16
- Anzahl Wendepole: 12
- Wirkungsgrad: 82,4%
- Wellendurchmesser Kommutatorseite: 300 mm
- Wellendurchmesser: Kupplungsseite: 300 mm
- Lagerdurchmesser Kommutatorseite: 250 mm
- Lagerlänge Kommutatorseite: 300
- Gewicht Stator: 30900 kg
- Gewicht Anker: 14000 kg
- Gesamtgewicht Motor: 44900 kg
- Kupplungstyp: starre Bolzenkupplung
- Kupplungsdurchmesser: 870 mm
- Anzahl Kupplungsbolzen: 10
- Durchmesser der Kupplungsbolzen: 70 mm
- Schlüsselweite Kupplungsbolzen 105 mm
Engagement für den Erhalt industrieller Geschichte
Die Interessengemeinschaft AL-Schacht kümmert sich mit viel Engagement um den Erhalt dieser technischen Anlage und macht sie für Besucher erlebbar. Wir laden Sie herzlich ein, sich vor Ort ein Bild von diesem eindrucksvollen Stück Bergbaugeschichte zu machen.